In maintenance; Seal coats or Topcoats are the best final set of coats to preserve the surface aesthatics & fundamentals of the intermediatory or the base coat materials.
There had been a strong reason why a scheduled maintainance of any coating material includes seal coats and crack filling.
It just doubles the life cycle of the system and provide maximum aesthatic appeal in fractions of the cost.
The key to effective crack filling and sealing is to repair and fill the cracks while they are just hair lined / small. The crack filling process eliminates the growth of cracks and inhibits new cracks from forming.
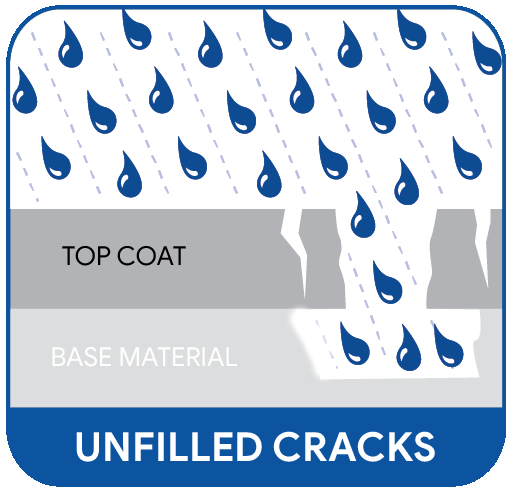
Why we always recommend to invest in maintenance ~ superior and robust Seal coats / Topcoats?
The logic goes like this, The Seal Coat / Topcoat goes in to the most abrasion and weathering effect while in the service life.
Once these seal coat or top coat gets damaged, the system becomes vulnerable and lets enviornmental factors such as moisture, carbonation and rains to let in.
This enviornmental material erodes the strucutral members such as Steel, Concrete, Asphalt, etc and aggrevates the material failures such as Pin Holes, debonding and lastly leads to failure of coatings.
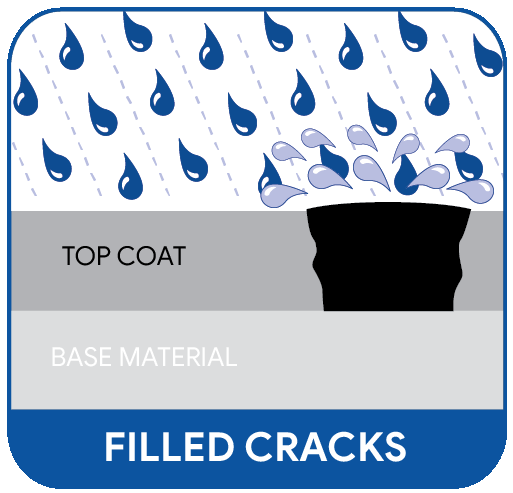
Filling these cracks with crack filler prevents these enviornmental factors from flowing throught the coating system and avoiding the erosion, corrosion or failure.
While blocking the passage of the water or moisture throught the coating system, it not only helps to lower the rate of deterioration but also increases the life of the coating system significantly.
While providing the estimates, system documentation and BOQ (bill of quantities) to the clients, we at Raja & Raja® also provide the SLA (Service Level Agreement) which clearly mentions the maintenance of the coating system is to be done at least Two times in a lifetime of the system.
Also, the selection of material for the particular site depending upon the geographic location, Environmental conditions the region has, type of structure on which system would be applied and lastly the application for which the coating system is being applied plays a significant role in deciding which products to be used.
Use of the over-engineered product increases the cost whereas the sub-standard product would fail in the service life of the coating system.
That’s the reason it is always called “PREVENTIVE MAINTENANCE” and is scheduled regularly (once a quater)